Are you frustrated by rough edges and long production time when cutting aluminum? Imagine making perfectly smooth cuts at lightning-fast speeds.
In this article we’ll discuss three convincing reasons why laser cutting may be the most effective technique for working with aluminium. Let go of old-fashioned methods and experience the accuracy and efficiency of lasers are the only option.
Prepare to discover the secrets of high-quality aluminum cutting and transform your production process. Let’s get started!
Understanding Aluminum Cutting Characteristics
Aluminum is an extremely versatile and extensively used material in a myriad of industries, however making it work efficiently requires a thorough understanding of its distinctive properties. The material is known for its lightweight and sturdy properties, it also has a comparatively low melting point, as well as extremely high conductivity to heat. These characteristics make it difficult to cut using traditional techniques, since they could result in rough edges, material warping and a slower time to produce.
The right method of cutting is essential to overcome the challenges. The speed, precision, and clear cuts made by laser cutting makes it the ideal choice to work with aluminum guaranteeing top-quality payoff and increased efficiency. In the next section we’ll look at three reasons that laser cutting is the best alternative for aluminum.
Why Should We Go With Laser to Cut Aluminum? 3 Reasons
Aluminum to laser cut is often considered superior to other cutting methods, including CNC machining or mechanical tools.
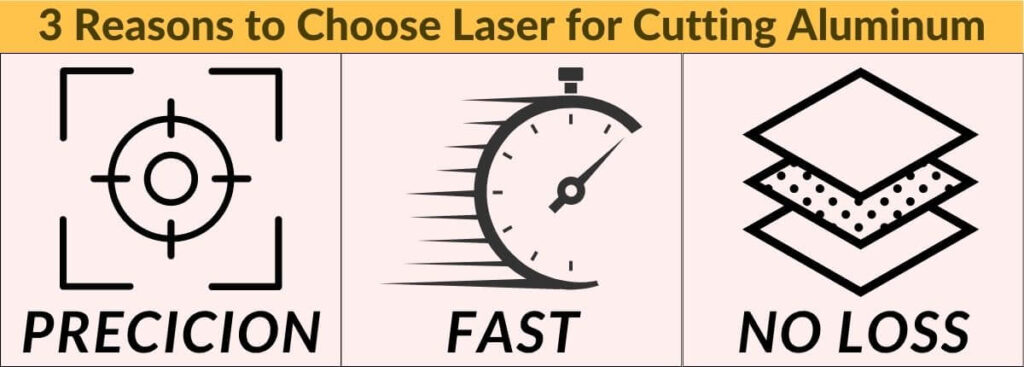
1. Precision and Accuracy
When the cutting of aluminum, precision becomes crucial. The traditional cutting techniques often struggle to fulfil the precise tolerances needed to produce high-quality items. However, laser cutting is a master at delivering unbeatable precision. Laser beams can be precisely controlled to produce intricate designs and precise cuts that have tolerances as small as +-0.1 millimeters.
A study conducted by the Fabricators & Manufacturers Association showed that businesses with laser cutting had a reduction of 15% in waste materials and 20 percent improve in efficiency of production. The combination of precision and effectiveness allows laser cutting to be the top option for professionals who work with aluminum.
2. High-Speed and Effective (High-speed cutting)
In today’s fast-paced production setting, efficiency has become the most important factor. Laser cutting provides substantial advantages in terms of productivity and speed when compared with conventional cutting techniques. Laser beam cutting can quickly slice through aluminium with incredible accuracy, reducing material processing time and maximizing the speed of production.
Studies have proven that laser cutting is as much as three times more efficient than traditional cutting techniques for aluminum. This speed improve outcome in shorter lead times and allows companies to meet deadlines and meet customer demands more energetically. Furthermore, laser cutting’s capability to work with complex designs and shapes without requirement for adjustments to the setup or tool increases its effectiveness.
Case Study:
A study carried out by a renowned manufacturing firm revealed a reduction of 25% in the time of production after switching to laser cutting of aluminum parts. This improved efficiency not only increased the manufacturing process, but it also brought about significant savings in costs and an rise in overall competitiveness.
Utilizing the speed and effectiveness that laser cutting offers, companies can streamline their processes, improve productivity, and remain ahead of today’s changing marketplace.
3. Clean and High-Quality Cuts
One of the primary advantages of using laser cutting on aluminum is the quality of the cuts it makes. Contrary to traditional methods of cutting which can result in rough edges and burrs laser cutting provides clear, precise cuts that have sleek edges and very little thermal distortion.
Case Study:
Studies have shown that laser cutting can significantly cut down the requirement for post-processing like deburring or sanding. This saves time as well as resources. This is particularly beneficial in fields where the quality of surface along with aesthetic appeal is essential like the consumer electronics industry and architecture.
Furthermore, the precise cuts that laser technology can make warrant the structure of aluminum components remains unaffected. This is crucial for any application that requires strong and durable components like aerospace components or automotive chassis. As long as the integrity is maintained to the materials, cutting with lasers adds in the quality overall and dependability that the product will be.
Conclusion
Laser cutting has emerged as the most effective solution to precision, efficiency and quality when cutting aluminum. From its unparalleled speed and precision to its high-quality cuts it makes laser cutting technology is revolutionizing the industry landscape.
Our exploration of laser cutting doesn’t need to stop here. Explore this world of laser-cutting to learn more about the latest techniques, insights and developments by looking through our other pieces on this fascinating topic.
Are you ready to take your aluminium cutting skills up a notch? Join us on this adventure of creativity and perfection. Find more articles about laser cutting and keep up-to-date in the field of manufacturing.
FAQs (Laser to Cut Aluminum)
1. When was Aluminum Foil Invented?
Aluminum foil was invented in 1910 by Swiss engineer Dr. Lauber, who filed for a patent in Switzerland that same year.
2. Where Was Aluminum Found?
Among the most common sources of aluminum is bauxite, a mineral found in tropical and subtropical regions such as Africa, the Caribbean, and Australia.
3. Can aluminum body panels be repaired?
You can repair aluminium body panels using specialized equipment and techniques like welding, dent removal, and surface refinishing.
4. What Is Aluminum Composite Panels?
Aluminium composite panels (ACP) are flat panels of two thin aluminium sheets bonded to a non-aluminium core. Building facades, signage, and interior design use them.
5. Can aluminum plates go in the microwave?
No, aluminium plates should not be used in the microwave as they can cause sparks and pose a fire hazard.