Laser and plasma cuttings are widely used in various industries to prune materials, primarily metal. Because of this, the question arises, what are the differences between laser cutting VS plasma cutting?
Laser cutting is generally more suitable for pruning thin materials or producing precise cuts. In contrast, the plasma-cutting process is better for pruning thicker materials or for trimming at high speed.
So, keeping in mind all your related queries about these terms, I will provide you with a detailed guide.
What is Laser and Plasma Cutting?
What is Laser Cutting?
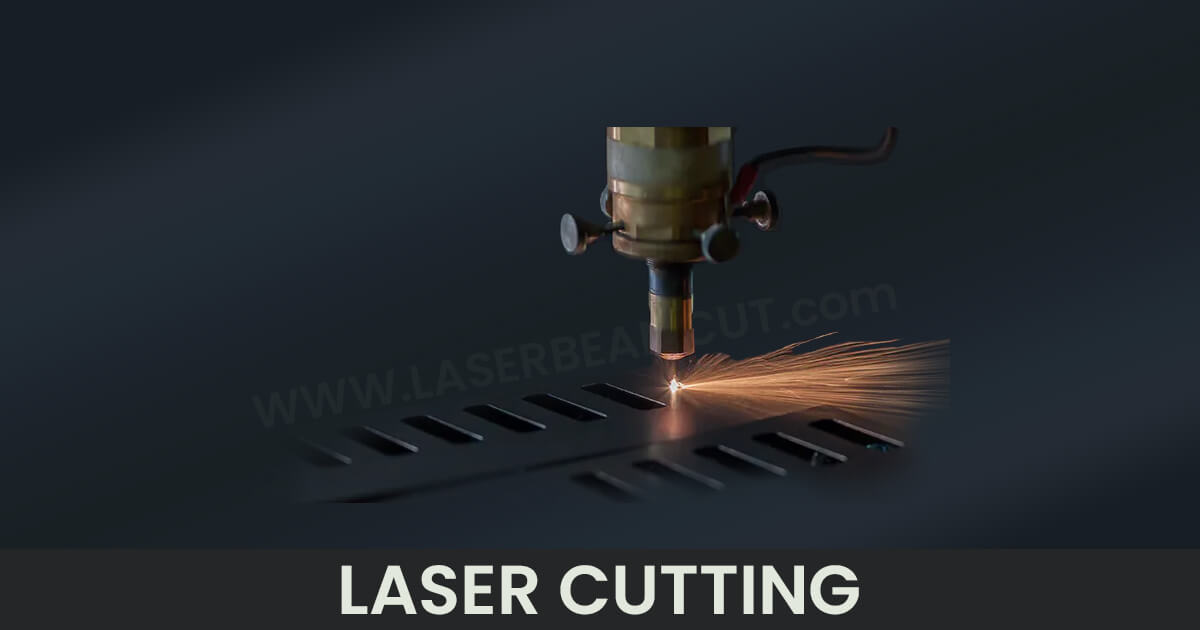
It is a manufacturing process that uses a focused beam of light to cut through the material. The laser generates the beam that is directed at the material by mirrors.
It is a highly accurate and precise method to cut metals. And it is capable of producing intricate cuts with minimal thermal distortion.
This cut process has various applications in various industries, including the aerospace, automotive, and construction industries. It is best for pruning complex shapes or producing small, precise parts.
Learn more about this topic by clicking here: What is laser cutting in detail?
What is Plasma-Cutting Process?
It is a manufacturing process that uses a high-velocity jet of ionized gas to cut through the material. The plasma is generated by heating a gas (usually air) to a very high temperature and then using an electrical current to ionize it.
This cut technique is fast and efficient and can easily prune thick metals. It has many applications in various industries, including automotive, construction, and other manufacturing industries. It is best to slice large pieces of metal or to prune metals at a fast rate.
However, it is not as precise as other methods, such as laser-cut pruning, and can produce more thermal distortion.
How Does it Work?
Here is a step-by-step breakdown of the plasma-cutting process:
- A Plasma-Torch is mounted above the material to cut on a cutting table.
- The gas supply is open, and the Plasma-Torch sucks the gas (usually air) into itself.
- An electrical current is applied to the electrode, creating an electrical arc within the torch. This arc ionizes the gas, creating a Plasma-Jet.
- The Plasma-Jet is directed at the material to cut, and the high-velocity plasma cuts through the material.
Types of Plasma-Cutter Machines
There are several types of plasma-cutter machines, which include:
Handheld cutters:
These cutters are portable devices that the operator uses to prune material manually. They are suitable for small-scale pruning tasks, in maintenance and repair work.
CNC Cutters:
These systems use computer numerical control (CNC) to guide the Plasma-Torch along predetermined path cuttings. They are suitable for trimming complex shapes and are often used in production environments.
Robotic Cutters:
These systems use robots to handle the Plasma-Torch and perform the cutting. They are suitable for high-volume pruning tasks.
Comparison of Laser Cutting VS Plasma Cutting
Here is a comparison of the two methods:
Parameter | Laser-Cutting VS Plasma-Cutter Process | Remarks | |
Speed | A Plasma-cutter is generally faster than a laser cutter, mainly when pruning thicker metals. | Plasma-Cutting is best. | |
Precision | Laser-cutter machines produce cleaner cuts with less thermal distortion than plasma-cutter machines. | Laser-Cutting is great. | |
Material Thickness | The plasma-cutting process can slice through thicker materials than the laser-cutting process. | Plasma-Cutting is best. | |
Cost | Laser-cut is generally more expensive than plasma-cut due to the cost of the laser equipment and the need for highly trained operators. | Laser-Cutting is expensive. | |
Material options | By both cut methods, you can cut a wide variety of materials, such as metal, wood, plastic, and composites. However, the plasma-cutting process is non-suitable for cutting thin materials, as the Plasma-Jet can cause them to warp or melt. | Both are best | |
Safety | A Laser-cutter produces a focused beam of light, which can be hazardous to the operator’s eyes. In plasma-cutting, if not using proper ventilation and protective equipment, it generates heat and harmful fumes, which can be risky for the environment. | Both need safety measures before doing their practical work. | |
Applications | Both have numerous applications, including the aerospace, automotive, and construction industries. Laser-cutting is generally more suitable for slicing thin metal or producing precise cuts. In contrast, plasma-cutting is better for pruning thicker metals or pruning at a faster rate. | Both have a wide range of applications. |
Plasma Cutting VS Laser Cutting VS Waterjet
By now, you are well aware of the terms plasma-cutting and laser-cutting process. Now have a look at the waterjet-cutting process.
Waterjet-cutting is a manufacturing process that uses a high-pressure jet of water to cut through the material. It is a precise pruning method to cut through a wide range of materials, including metals, stones, and composites. Waterjet produces minimal thermal distortion but is slower than other pruning methods. It is not suitable for pruning thick metals.
Conclusion:
I hope you are now well aware of comparing Laser cutting VS Plasma Cutting. In conclusion, both are two popular methods for material cuttings that have pros and cons of each procedure.
The Laser-Cuttings are more precise and produce cleaner cuts with minimal thermal distortion, but it is slower and more expensive than Plasma-Cuttings. Plasma-cutting is faster and capable of slicing through thicker metals, but it is not as precise as Laser-Cuttings and can produce more thermal distortion.
Both methods have many applications and are used to prune many materials. Laser-cutting is generally more suitable for slicing thin metals or producing precise cuts. In contrast, Plasma-Cutting is better for trimming thicker materials or for pruning at a faster rate.
FAQs ( Frequently Asked Questions ):
1: How to choose laser-cutting or plasma-cutting processes for our tasks?
Consider a few parameters when need to choose the material-cutting procedure.
- Precision needed
- Speed
- Cost
- Material options
- Safety
- Application requirements
2. What are the five advantages of using a laser-cutter machine?
Five advantages of using a laser-cutters are:
- High precision
- Minimal thermal distortion
- Ability to prune complex shapes
- Ability to slice a wide range of metals
- High prune speeds for thin metals
3. What are the five advantages of using a plasma-cutter machine?
Five advantages of using these cutters are:
- Ability to slice through thick metals
- High prune speeds
- Versatility
- Low cost,
- Ability to prune a wide range of metals.
4. What materials are not possible to prune with a plasma-cutter machine?
Plasma-cutters cannot cut through non-conductive materials such as aluminum, brass, and copper, as these materials do not conduct electricity. These are also not suitable for slicing thin metals.
5. Which material should you never cut in the laser-cutter machine?
Materials that produce toxic fumes during the cut, such as PVC or plastics, are not possible with laser-cutter machines. These materials release harmful fumes, which can be dangerous to inhale.